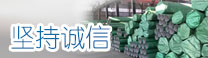
行業(yè)動(dòng)態(tài)
聯(lián)系方式
聯(lián)系人: 劉經(jīng)理
手 機(jī) :136 7673 1206
電 話 : 0577-28909778
E-mail : myzhide@126.com
厚壁不銹鋼管
您的位置:網(wǎng)站首頁(yè) > 新聞動(dòng)態(tài) > 厚壁不銹鋼管 > 正文熱處理工藝對(duì)7Cr17MoV馬氏體不銹鋼組織性能的影響
采用金相顯微鏡、掃描電鏡、洛氏硬度計(jì)、沖擊試驗(yàn),觀察和分析了7Cr17MoV馬氏體不銹鋼在990~1110℃淬火+180~220℃回火的組織和性能變化。結(jié)果表明:淬火組織為殘留奧氏體和碳化物分布于馬氏體基體上。隨淬火溫度的升高,殘留奧氏體含量和馬氏體過(guò)飽和度增加,針狀馬氏體組織變粗,1080℃淬火硬度升高到最大值62.5HRC。沖擊試驗(yàn)結(jié)果表明:隨回火溫度逐漸升高,試樣硬度有部分下降,但韌性顯著提高,200~220℃時(shí)韌性最佳,達(dá)到19J/cm2。綜合硬度和韌性考慮,最佳熱處理工藝為1080℃淬火+200~220℃回火。鹽霧試驗(yàn)表明:1080℃淬火+200℃回火后腐蝕率小于4%,符合使用要求。
不銹鋼作為一種用途廣泛的鋼,具有良好的耐蝕性、耐熱性、低溫強(qiáng)度和機(jī)械特性,廣泛應(yīng)用于餐具、醫(yī)學(xué)用具、試驗(yàn)用具、裝飾品等。近百年的發(fā)展使得不銹鋼可提供各種特殊性能,滿足不同的服役條件和生產(chǎn)制造的要求。不銹鋼按照組織狀態(tài)可分為馬氏體型不銹鋼、鐵素體型不銹鋼、奧氏體型不銹鋼、雙相不銹鋼和沉淀硬化型不銹鋼,其均具有良好的耐蝕性,可在腐蝕介質(zhì)中保持良好的力學(xué)性能。
不銹鋼中發(fā)展最早的就是馬氏體不銹鋼,按成分可分為Cr系(400系列)、Cr-Ni系(300系列)、Cr-Mn-Ni(200系列)及析出硬化系(600系列)。7Cr17馬氏體不銹鋼因含碳量較高,可以在熱處理以后達(dá)到較高的強(qiáng)度、硬度、耐磨性和沖擊韌度,用于力學(xué)性能要求較高、耐蝕性能要求一般的一些零件上,如彈簧、汽輪機(jī)葉片、水壓機(jī)閥等。其中高Cr含量(11.5%~18%)是不銹鋼耐腐蝕的重要原因,加入約1%Mo及0.1%V,可以增加7Cr17鋼的耐磨性及耐蝕性,從而形成應(yīng)用相當(dāng)廣泛的馬氏體不銹鋼7Cr17MoV,這類(lèi)鋼是在淬火、回火后使用的。與其類(lèi)似的鋼種有美國(guó)ASTM440A和日本SUS440A,主要用于制作高硬度、高耐磨性的中高檔刀剪產(chǎn)品和醫(yī)療器械。鑒于國(guó)內(nèi)對(duì)此類(lèi)鋼的熱處理研究較少,為充分發(fā)揮7Cr17MoV馬氏體不銹鋼的特性,提高產(chǎn)品質(zhì)量,本文研究了熱處理工藝參數(shù)對(duì)7Cr17MoV硬度、沖擊韌度及組織性能的影響,為生產(chǎn)應(yīng)用提供理論依據(jù)[2]。
1試驗(yàn)材料、設(shè)備及試驗(yàn)方法
1.1試驗(yàn)材料及設(shè)備
試驗(yàn)用原材料為厚10mm的7Cr17MoV馬氏體不銹鋼鋼板,其化學(xué)成分見(jiàn)表1。供貨狀態(tài)為750℃退火態(tài),初始組織為鐵素體+球狀合金碳化物,硬度為220HB(約17HRC)。
用線切割機(jī)將不銹鋼板切割成55mm×10mm×10mm的標(biāo)準(zhǔn)V型夏比沖擊試樣48個(gè),試樣分成兩組,A組為空白試樣(3個(gè)試樣,編號(hào)01#);B組為熱處理試樣(45個(gè)試樣,編號(hào)分別為02#~16#)。
本文主要研究馬氏體不銹鋼的硬度、韌性和耐腐蝕性等性能。硬度測(cè)試使用HR-150A洛氏硬度計(jì),加載砝碼150kg,每個(gè)測(cè)5次,舍棄最大值和最小值,取余下3次的平均值作為最終結(jié)果。V型缺口沖擊試驗(yàn)在室溫下利用JB-300擺錘式?jīng)_擊試驗(yàn)機(jī)上進(jìn)行,3次重復(fù)性試驗(yàn)取試驗(yàn)平均值作為最終結(jié)果。鹽霧試驗(yàn)采用5%的NaCl溶液模擬大氣腐蝕。金相試驗(yàn)采用DMIE200M金相顯微鏡進(jìn)行金相組織觀察。斷口形貌采用ZeissEVOMA15掃描電鏡觀察,并采用OxfordInstrument能譜儀進(jìn)行微區(qū)成分分析。
1.2試驗(yàn)方法
(1)首先將A組試樣作為空白試樣,分別進(jìn)行硬度、沖擊韌度測(cè)試以及鹽霧試驗(yàn)測(cè)試。
(2)將B組進(jìn)行5(淬火)×3(回火)正交熱處理試驗(yàn)。為正確制定鋼的熱處理工藝,參照法國(guó)澎湃旗斯鋼鐵公司提供的T7Mo鋼的熱處理工藝(Air1060℃59~60HRC,回火200℃,56~58HRC)。淬火溫度990~1110℃,間隔30℃,保溫25min,油淬,立即測(cè)試各試樣硬度并記錄。然后進(jìn)行180、200和220℃回火處理,保溫2h,空冷,立即進(jìn)行沖擊硬度測(cè)試和沖擊韌度試驗(yàn)并記錄數(shù)據(jù)。
(3)選取性能兼優(yōu)(硬度和沖擊韌度兼優(yōu))作為B組優(yōu)化工藝試樣Bopt,對(duì)其進(jìn)行鹽霧試驗(yàn)。
(4)分析對(duì)比空白試樣A與Bopt的硬度、沖擊韌度和耐腐蝕性能,利用理論解釋這一性能轉(zhuǎn)變的原因。具體方法有金相試驗(yàn)分析成分、組織及結(jié)構(gòu);SEM觀察表面形貌并進(jìn)行微區(qū)成分分析。
2試驗(yàn)結(jié)果及分析
2.1熱處理工藝對(duì)試樣硬度的影響
2.1.1淬火工藝對(duì)試樣硬度的影響
分別對(duì)原始退火態(tài)試樣、990~1110℃淬火后的試樣進(jìn)行硬度測(cè)試記錄,取每大組9個(gè)試樣的平均值作為最終淬火硬度。空白試樣A硬度平均值約17HRC,圖1為不同淬火溫度后試樣硬度變化趨勢(shì)?芍,7Cr17MoV淬火后,隨淬火溫度的升高,其硬度先增加后降低。990~1020℃淬火時(shí),試樣硬度的變化取決于大量未溶碳化物顆粒的大小、數(shù)量、鐵素體的含量,一些元素如碳、鉻、鉬、釩在組織中的溶解度比較低,在急冷后,存留在馬氏體中的碳及某些合金元素含量偏低,導(dǎo)致淬火硬度不高。隨淬火溫度升高,固溶在鋼中的碳和合金含量開(kāi)始上升,同時(shí)鋼中馬氏體過(guò)飽和度增加,導(dǎo)致馬氏體轉(zhuǎn)變后的硬度愈高,淬火硬度愈高,在1080℃左右達(dá)到峰值62.5HRC,說(shuō)明碳化物顆粒均基本溶解,剩余的均勻分布,已基本奧氏體化,合金化程度高,故硬度比較高。但淬火溫度進(jìn)一步升高時(shí),組織中含碳量及合金含量過(guò)高,導(dǎo)致晶粒長(zhǎng)大,奧氏體越穩(wěn)定,冷卻轉(zhuǎn)變后殘余奧氏體量增加,淬火硬度反而有所下降。7Cr17MoV中碳、鉻、鉬、釩的增加使鋼的Ms點(diǎn)降低,馬氏體形核減少,也會(huì)導(dǎo)致殘余奧氏體量增加,從而硬度急劇下降至60HRC。
2.1.2回火工藝對(duì)硬度的影響
在180、200和220℃回火處理時(shí),試樣的硬度隨回火溫度的升高緩慢下降1~5HRC,表現(xiàn)出較好的回火穩(wěn)定性。這是由于7Crl7MoV鋼中含有17%Cr和一定量的鉬和釩等合金元素,且鉻、鉬、釩都是強(qiáng)碳化物形成元素,阻礙了鋼中碳原子的擴(kuò)散,延遲了鋼在回火時(shí)的組織轉(zhuǎn)變過(guò)程,推遲了馬氏體的分解和殘余奧氏體的轉(zhuǎn)變[4]。1080℃淬火時(shí)不同溫度回火后的硬度見(jiàn)表2。
對(duì)7Cr17MoV進(jìn)一步做300、400、500及600℃高溫回火發(fā)現(xiàn),低溫回火硬度逐漸降低,幅度不大,300℃回火時(shí)硬度最低為56.3HRC,500℃回火后硬度增大至57.5HRC,隨后又降低,硬度曲線呈馬鞍狀。500℃回火時(shí)硬度增加是由于7Cr17MoV材料中具有較高含量的鉻,同時(shí)含有鉬、釩等合金元素。這些元素屬于強(qiáng)碳化物形成元素,在滲碳體中大量存在。當(dāng)回火溫度到達(dá)一定區(qū)間內(nèi),這些強(qiáng)碳化物形成元素在滲碳體中聚集到某一濃度后將發(fā)生轉(zhuǎn)變,形成特殊碳化物。與滲碳體相比,這些特殊碳化物的硬度更高,以高度彌散的顆粒存在于基體中,不易聚集長(zhǎng)大,其沉淀硬化導(dǎo)致了材料的硬度升高。但高溫回火會(huì)產(chǎn)生馬氏體的分解與合金碳化物的析出,鋼的組織呈屈氏體組織,防銹性能下降,故7Cr17MoV應(yīng)采用低溫回火來(lái)提高韌性并減少硬度損失。
2.2熱處理工藝對(duì)沖擊韌度的影響
沖擊韌度試驗(yàn)數(shù)據(jù)顯示,退火態(tài)7Cr17MoV沖擊韌度為15J/cm2,淬火及200℃回火后的沖擊韌度如表3所示。
淬火后,相對(duì)于退火態(tài)母材試樣沖擊韌度急劇減小,試驗(yàn)數(shù)據(jù)顯示最低至7J/cm2,后經(jīng)回火,沖擊韌度又急劇增加至19J/cm2。由表3可知,經(jīng)淬火、回火后,沖擊韌度隨淬火溫度升高先增大,超過(guò)1080℃后又減小。退火時(shí)球化處理可以改變碳化物的微觀組織形貌和分布,使組織更加均勻,同時(shí)對(duì)減少淬火加熱中的熱敏型和變形都有較好的作用。
淬火時(shí),由于較高的淬火溫度,導(dǎo)致淬火后晶粒粗大,油淬急冷奧氏體轉(zhuǎn)變成馬氏體,硬度急劇增加,使材料韌性下降至7J/cm2。此外,在淬火冷卻時(shí),由于較快的冷卻速度,材料會(huì)出現(xiàn)應(yīng)力集中現(xiàn)象,從而會(huì)導(dǎo)致材料的韌性急劇降低;鼗鸬闹饕康氖墙档突蛘呦龖(yīng)力,確保組織穩(wěn)定轉(zhuǎn)變過(guò)程,提高鋼的塑性和韌性,獲得硬度、強(qiáng)度、韌性的適當(dāng)搭配。因此,在回火后,材料的韌性得到了大幅度提升,在200~220℃回火提升至19J/cm2。
2.3熱處理對(duì)耐蝕性的影響
鹽霧試驗(yàn)(NSS)是在模擬某些特定的潮濕氣候的環(huán)境下,來(lái)考查產(chǎn)品、材料及其防護(hù)層的抗鹽霧腐蝕能力的試驗(yàn)。人工模擬鹽霧環(huán)境試驗(yàn)是在一種具有一定容積空間的試鹽霧試驗(yàn)箱下進(jìn)行。在箱體內(nèi)造成鹽霧環(huán)境對(duì)馬氏體不銹鋼的耐鹽霧腐蝕性能質(zhì)量進(jìn)行考核。其鹽霧環(huán)境下的氯化物的鹽濃度是天然環(huán)境鹽霧含量的幾倍或幾十倍,這使得腐蝕速度大大提高,可大大減少對(duì)兩種材料進(jìn)行鹽霧試驗(yàn)的時(shí)間,在天然環(huán)境下對(duì)這兩種材料試驗(yàn)進(jìn)行試驗(yàn)腐蝕要1年的時(shí)間,在人工模擬鹽霧環(huán)境條件下試驗(yàn)就只要24h,兩者得到的結(jié)果很相似。
圖2為7Cr17MoV在1080℃淬火+200℃回火后的腐蝕圖。從圖中及相關(guān)文獻(xiàn)中可知,試樣表面出現(xiàn)了一定數(shù)量的點(diǎn)蝕,沒(méi)有出現(xiàn)明顯的氣泡、裂紋等缺陷。對(duì)材料進(jìn)行腐蝕速率的評(píng)級(jí),是將材料的主要表面劃分成5mm×5mm的小格子,通過(guò)觀察材料的被腐蝕處占小格子數(shù)量的百分比來(lái)評(píng)級(jí)。根據(jù)腐蝕形貌圖分析得出,7Cr17MoV的腐蝕率小于4%,屬于5級(jí)標(biāo)準(zhǔn),試樣表面腐蝕坑的尺寸大小和數(shù)量都符合要求。這表明在經(jīng)過(guò)此熱處理加工工藝后的耐蝕能力是符合要求的。
2.4熱處理對(duì)材料組織的影響
圖3為7Cr17MoV鋼1080℃淬火及不同溫度回火后的金相組織。
從上面幾個(gè)金相圖及母材狀況中可以看出,這些組織為馬氏體+殘余奧氏體+碳化物。7Cr17MoV鋼材在球化退火處理時(shí),使片層珠光體轉(zhuǎn)變?yōu)榍驙钪楣怏w。這種珠光體對(duì)淬火加熱時(shí)奧氏體的形成、滲碳體的溶解、固溶體的碳含量和合金元含量以及奧氏體晶粒的長(zhǎng)大與形成都有影響。材料成分分布的均勻性也是影響工件性能的因素之一。在淬火加熱時(shí),均勻的球狀珠光體可以得到細(xì)小的奧氏體晶粒。隨加熱溫度的升高,晶粒長(zhǎng)大傾向相對(duì)減少。因?yàn)榻M織中的碳化物晶粒將變得細(xì)小,其分布也均勻化。在奧氏體化時(shí),這些未溶解碳化物將作為核點(diǎn),起到形核長(zhǎng)大、細(xì)化組織的作用。隨淬火溫度進(jìn)一步提升,這些球化的滲碳體溶解速度降低,在奧氏體中碳與合金元素含量開(kāi)始減少,這就導(dǎo)致了淬火后材料的硬度降低。而淬火后得到的組織為板條馬氏體。從馬氏體和奧氏體的相含量隨回火溫度的變化來(lái)看,基體組織變化主要是由于殘余奧氏體在不同回火溫度下轉(zhuǎn)變的量不同。同時(shí),析出相碳化物對(duì)力學(xué)性能有較大影響。對(duì)比幾個(gè)圖得知,隨回火溫度升高,組織中的碳化物晶粒先減小后增大,且在200~220℃回火時(shí)更加細(xì)小,其彌散效應(yīng)保證了組織擁有足夠的硬度和韌性。同時(shí),組織分布更加均勻,7Cr17MoV這種鋼材的碳含量為0.7%左右,內(nèi)應(yīng)力較小,所以在較低的溫度下回火,就能去除組織的應(yīng)力,改善組織的塑韌性,且保持組織在淬火后的高硬度。
2.5沖擊斷口SEM觀察
圖4為母材及不同溫度淬火+回火處理以后7Cr17MoV的沖擊試樣的斷口形貌。可看到斷口有韌窩和細(xì)小的微孔以及第二相粒子;且可看出斷口呈微孔聚集韌斷形式,斷裂前期,位錯(cuò)運(yùn)動(dòng)在第二相粒子處塞積,由于應(yīng)力集中導(dǎo)致界面分離,形成微孔,微孔連接并長(zhǎng)大最終發(fā)展斷裂,從而形成斷口韌窩狀。沒(méi)經(jīng)過(guò)淬火+回火處理的母材斷口韌窩很小,且第二相粒子很多,因此導(dǎo)致裂紋源很多,韌性不高。而1080℃淬火的斷口形貌相對(duì)于1010℃淬火的斷口明顯更大更深,由于韌窩是在裂紋形成和擴(kuò)展過(guò)程中塑性變形而形成的,故變形越大,吸收的沖擊功越多,因而沖擊韌度越好。
3結(jié)論
(1)7Cr17MoV馬氏體不銹鋼在990~1110℃淬火時(shí),硬度先增加后減小,且在1080℃出現(xiàn)峰值,最大硬度可達(dá)62.5HRC;沖擊韌度則隨淬火溫度升高逐漸降低,在1100℃淬火后急劇降低至7J/cm2左右。
(2)7Cr17MoV馬氏體不銹鋼在180~220℃回火時(shí),硬度減小緩慢,呈現(xiàn)出較好的回火穩(wěn)定性;韌性則有較大提升,在200~220℃時(shí)韌性最佳,最高至19J/cm2。
(3)在鹽霧試驗(yàn)后7Cr17MoV馬氏體不銹鋼出現(xiàn)一定數(shù)量的點(diǎn)蝕。根據(jù)腐蝕速率評(píng)級(jí)標(biāo)準(zhǔn),7Cr17MoV的腐蝕率小于4%,屬于5級(jí)標(biāo)準(zhǔn),符合生產(chǎn)使用要求。
(4)7Cr17MoV馬氏體不銹鋼合理的熱處理工藝為750℃退火+1080℃淬火+200~220℃回火。
文章作者:不銹鋼管|304不銹鋼無(wú)縫管|316L不銹鋼厚壁管|不銹鋼小管|大口徑不銹鋼管|小口徑厚壁鋼管-浙江至德鋼業(yè)有限公司
文章地址:http://hzsnkyy.cn/Info/View.Asp?Id=989
版權(quán)所有 © 轉(zhuǎn)載時(shí)必須以鏈接形式注明作者和原始出處
我們需要您的支持與分享
相關(guān)新聞
- 沒(méi)有資料