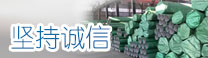
行業(yè)動態(tài)
聯(lián)系方式
聯(lián)系人: 劉經(jīng)理
手 機 :136 7673 1206
電 話 : 0577-28909778
E-mail : myzhide@126.com
厚壁不銹鋼管
您的位置:網(wǎng)站首頁 > 新聞動態(tài) > 厚壁不銹鋼管 > 正文不銹鋼管焊接內(nèi)部缺陷成因及預防
在不銹鋼管焊接過程中,由于人員、設(shè)備、材料、方法、環(huán)境等各方面因素影響,在不銹鋼管焊縫處產(chǎn)生缺陷。不銹鋼管焊接內(nèi)部缺陷主要有裂紋、氣孔、夾渣、未焊透、未熔合等。
一、裂紋。
在焊縫或熱影響區(qū)內(nèi)開裂形成的縫隙叫裂紋。分為冷錢紋、熱裂紋、再熱裂紋等。焊接裂紋危害性很大,它除了降低焊縫強度外,還因裂紋末端存在尖銳的缺口,而引起嚴重的應力集中,造成結(jié)構(gòu)斷裂破壞
1、冷裂紋:焊縫冷卻過程中,溫度在200℃以下產(chǎn)生的裂紋,叫冷裂紋。
1.1產(chǎn)生原因
焊縫在結(jié)晶過程中,氫含量過高不能逸出,聚集在離熔合線附近的熱影響區(qū)中;母材的淬硬傾向大,在冷卻速度較快的條件下,熱影響區(qū)形成脆而硬的馬氏體組織:焊接過程中由于工件局部不均勻受熱,焊縫在冷卻過程中會產(chǎn)生很大的拉應力,這種拉應力隨焊縫溫度的下降而增大。在氫、淬硬組織、應力三個因素共同作用下,即產(chǎn)生裂紋。
1.2預防措施
1.2.1合理選擇焊材。選用低氫型焊條,減少含氫量,焊前嚴格按規(guī)定進行烘干,焊口邊緣徹底清理干凈,減少氫的來源;選用合適焊材,使焊縫與母材有良好的匹配,增加焊縫金屬的塑性,不產(chǎn)生任何不良組織,如晶粒粗化及硬脆馬氏體等
1.2.2選擇合理的焊接工藝。如焊前預熱、控制層間溫度、減緩冷卻速度,使用小電流、分散焊等措施減小輝件的溫度差,改善焊縫及熱影響區(qū)的組織狀態(tài)等
1.2.3焊后及時熱處理。使氫能從焊縫中逸出、減少焊接殘余應力及改善接頭的組織和性能。
1.2.4采用合理的焊接順序和焊接方向,改善焊接的應力狀態(tài),降低焊接殘余應力。
1.2.5制定合理的成形加工和組裝工藝,盡可能減小冷卻變形度,避免強制組裝,預防組裝過程中造成各種傷痕。
2、熱裂紋:熱裂紋是在稍低于凝固溫度下產(chǎn)生的裂紋。
在300℃以上高溫產(chǎn)生的裂紋都叫熱裂紋。熱裂紋大多產(chǎn)生在焊縫中,有時也出現(xiàn)在熱影響區(qū)內(nèi)。這類裂紋沿晶界開裂,斷面上大多有明顯氧化色彩。
2.1產(chǎn)生原因:熱裂紋是拉應力和低熔點共晶兩者聯(lián)合作用形成的裂紋。無論增大那一方面的作用,都可以促使焊縫中形成熱裂紋。
2.2預防措施
2.2.1控制化學成分,限制易生成低熔點共晶物和有害雜質(zhì)的含量,應減少焊縫金屬中的鎳、碳、硫、磷含量,增加鉻、鉬、硅及錳等元素,可以減少熱裂紋的產(chǎn)生。
2.2.2改善焊縫金屬組織,細化晶粒,減少或分散偏析,降低低熔點共晶物的有害作用2.2.3選用適當?shù)暮笚l藥皮類型。用低氫型藥皮焊條可以使焊縫晶粒細化,減少雜質(zhì)偏析,提高抗裂性。用酸性藥皮焊條氧化性強,便合金元素燒損多,抗裂性下降,而且品粒粗大,使熱裂紋極易產(chǎn)生。
2.2.4控制焊縫形狀,盡量得到焊縫成形系數(shù)較大的焊縫。
2.2.5采用多層多道焊法,控制層問溫度,避免偏析物案集在焊縫中心部位。
2.2.6焊前預熱,減小冷卻速度,降低應力。
2.2.7焊接收弧熔池應填滿,減少弧坑裂紋。
2.2.8選擇合理的焊接順序和焊接方向,減小焊接應力。
2.2.9采用小電流、快焊速來減少焊接熔池過熱、快速冷卻,以減少偏析,使抗裂性提高。
3、再熱裂紋:
再熱裂紋是焊后焊件在一定溫度范圍再次加熱,如焊后熱處理或其他加熱過程產(chǎn)生的裂紋。焊后熱處理裂紋發(fā)生于焊后應力消除熱處理的加熱過程中。再熱裂紋起源于熱影響的粗品區(qū)和焊根部位,具有晶間斷袋的特征。
3.1產(chǎn)生原因
3.1焊縫再次加熱后,由第一次熱過程所形成的過飽和固熔碳化物再次被析出,即析出沉淀碳化物,造成晶內(nèi)強化,使滑移應變集中于原奧氏體晶界。當晶界的塑性應變能力不足以承受松弛應力過程所產(chǎn)生的應變時,則產(chǎn)生再熱裂紋。
3.1.2接頭在焊后熱處理中,易使剛脆化的元素集結(jié)在晶界上,削弱了晶界的結(jié)合力,產(chǎn)生再熱裂紋。
3.2 防措施
3.2.1減小熱影響區(qū)的過熱傾向,細化奧氏體晶粒尺寸。
3.2.2選用合適的焊接材料,提高金屬在消除應力熱處理溫度時的塑性,以提高承擔松地應變的能力。
3.2.3提高預熱溫度、焊后采取緩冷,并使焊縫外形均勻平,以減小焊接殘余應力和應力集中。
3.2.4采用正確的熱處理規(guī)范和工藝,盡量不在熱敏感區(qū)停留過長。
二、氣孔:
氣孔是焊接時熔池中的氣體未來得及從焊縫內(nèi)逸出,而殘留在焊縫中的空穴。
1、產(chǎn)生原因
1.1坡口兩側(cè)不做清理或清理不干凈,熔池冶金過程中,非金屬元素形成非金屬氧化物,由于氣體在金屬中的溶解度隨溫度降低而減少,在結(jié)晶過程中部分氣體來不及逸出,氣泡殘留在金屬內(nèi)形成了氣孔
1.2焊接電弧過長保護不好、焊條受潮、管內(nèi)有穿堂風等,增大了氣體侵入熔他機會。
1.3焊接電流過小,焊接速度過快,熔敷金屬粘度大,影響氣體從熔池中逸出。
1.4,塔地溫度過高,產(chǎn)生沸騰現(xiàn)象,氣體不能全部從熔池中排除
1.5卻鏈金屬中吸入了過多的如組氣、一化碳、氮氣等氣體。
2、預防措施
2.1在焊接前,應檢查管口及其兩側(cè)的油、銹等污物是否清理干凈。在使用焊絲前,應對焊絲表面的油污、水分、銹斑等污物徹底清除。
2.2不得使用藥皮開裂,剝落、變質(zhì)、偏心或焊芯嚴重腐蝕的焊條。
烘烤.
2.3焊條和焊劑使用前,應按規(guī)定要求進行2.4焊接時應選用合適的焊接電流和焊接速度,采用短弧焊接。對合金鋼及厚壁碳素鋼應來取焊前預熱,這樣可減慢熔池的冷卻速度,有利于氣體的充分逸出,避免產(chǎn)生氣孔缺陷.
2.5焊接時應避免風吹雨淋等惡劣天氣環(huán)境影響。焊工在露天作業(yè)時,應設(shè)置防風防雨雪的裝置。焊接管子時,要注意管內(nèi)穿堂風的影響。
2.6在進行氣體保護焊時,要檢查好氣體的純度和含水量是否符合有關(guān)標準要求;控制氬氣流量。
2.7-焊前預熱可減緩熔池冷卻速度,及焊后熱處理等,有利于氣體逸出.
三、夾渣:
夾渣是焊縫金屬中存在的非金屬夾雜物或
1、產(chǎn)生原因
1.1焊接電流過小或運條速度過快,金屬熔池溫度較低,液態(tài)金屬和熔渣不易分開,或熔渣未來得及浮出,熔池已開始凝固,有時也存在清根不徹底問題。
1.2母材中的夾渣混入到焊縫中,焊條藥皮中難熔物,及坡口邊緣氧化皮、鐵銹和焊接過程中的熔渣等末清理干凈,滯留在熔化金屬中。
1.3焊接過程的冶金產(chǎn)物(如氧化物、硫化物、氮化物等)殘留在焊縫中。
2、預防措施
2.1嚴格清理不銹鋼管坡口及其附近表面污物、氧化渣,徹底清理前一道焊道的熔渣,預防外來夾渣混入
2.2,選用適的焊接電流,減緩焊接速度,預防焊縫金屬冷卻過快,以使熔渣充分浮出。
2.3正確運條,有規(guī)律的擺動焊條,攪拌熔池中的液態(tài)金屬,促進烙渣與鐵水良好分離。
2.4選擇性能良好的焊材,焊材保持清潔,有利于預防夾產(chǎn)生
四、末焊透:
未焊透是兩母材之間、焊道之間、或母材與焊道之間出現(xiàn)熔化金屬適度不好的現(xiàn)象。
1、產(chǎn)生原因
1.1,對口間隙太小,鈍邊太大,焊接電流太小,運條太快。
1.2焊接環(huán)境溫度低,焊件散熱太快,焊接熱輸入量小
1.3焊條角度不當,或電弧發(fā)生偏吹。
1.4運條不當,熔深不夠.
2、預防措施
鈍邊量。
2.1接口對齊,間隙合適,坡口控制合理的
2.2選用合適選規(guī)格的焊材。
2.3選擇合適的焊接電流。
2.4焊工操作方法得當。
五、未熔合:
未熔合是熔敷金屬與母材之間未熔融,也叫粘合。焊縫根部三角未焊透屬于未熔合的一種。
1、產(chǎn)生原因
1.1坡口與母材未清理干凈。
1.2坡回存在氧化物和污物,使熔敷金屬與母材未熔融。
1.3焊接電流太小,運條角度不當。
2、預防措施
2.1重視坡口和母材的清理。
2.2選擇合理的焊接規(guī)范。
2.3正確的操作工藝。
2.4注意焊件的預熱溫度。
焊接是不銹鋼管安裝的一項關(guān)鍵工作,其質(zhì)量的好壞直接影響到工程的安全運行和使用壽命。由子不銹鋼管焊接內(nèi)部缺陷存在于焊縫內(nèi)部,不能從外表發(fā)現(xiàn),只有通過無損探傷或破壞性檢驗才能發(fā)現(xiàn),因此必須采取嚴格的控制措施,保證不銹鋼管的焊接質(zhì)量,確保優(yōu)質(zhì)安裝工程的實現(xiàn)。
文章作者:不銹鋼管|304不銹鋼無縫管|316L不銹鋼厚壁管|不銹鋼小管|大口徑不銹鋼管|小口徑厚壁鋼管-浙江至德鋼業(yè)有限公司
文章地址:http://hzsnkyy.cn/Info/View.Asp?Id=1043
版權(quán)所有 © 轉(zhuǎn)載時必須以鏈接形式注明作者和原始出處
我們需要您的支持與分享
相關(guān)新聞
- 沒有資料